Dieser Hamburger verändert mit seiner Arbeit die Welt
Häuser aus dem Drucker, Brücken aus dem Drucker, Flugzeugteile aus dem Drucker – die 3D-Fertigungstechnologie revolutioniert immer mehr die Welt. Hamburg nimmt bei dieser Entwicklung eine führende Position ein. Denn das Fraunhofer Institut für Additive Produktionstechnologie in Bergedorf liegt dabei ganz weit vorn. Den Forschern geht es vor allem um eins: ums Klima!
Das Ding vorne in der Vitrine sieht ein bisschen aus wie eine Koralle. Verschiedene Röhren ragen unterschiedlich hoch nach oben. Tatsächlich handelt es sich bei dem merkwürdigen Gebilde um einen Hydraulikblock für einen Airbus A340. Das Besondere: Das für den Flugzeugantrieb wichtige Teil ist mit einem 3D-Drucker Schicht für Schicht aufgebaut worden. Und: Es ist 30 Prozent leichter als sein Vorgänger, den man früher aus einem Metallblock herausgefräst hat!
Hamburger Institut: Klimaschutz durch Gewichtsreduzierung
Genau diese Gewichtsreduzierung ist es, die den Forschern so am Herzen liegt. „Weniger Gewicht bedeutet weniger Energieverbrauch“, erklärt Professor Ralf Eckhard Beyer, Leiter des Fraunhofer Instituts. Wenn das Flugzeug leichter ist, verbraucht es weniger Kerosin. Das gleiche gilt für Schiffe, Züge, Autos oder Raketen.
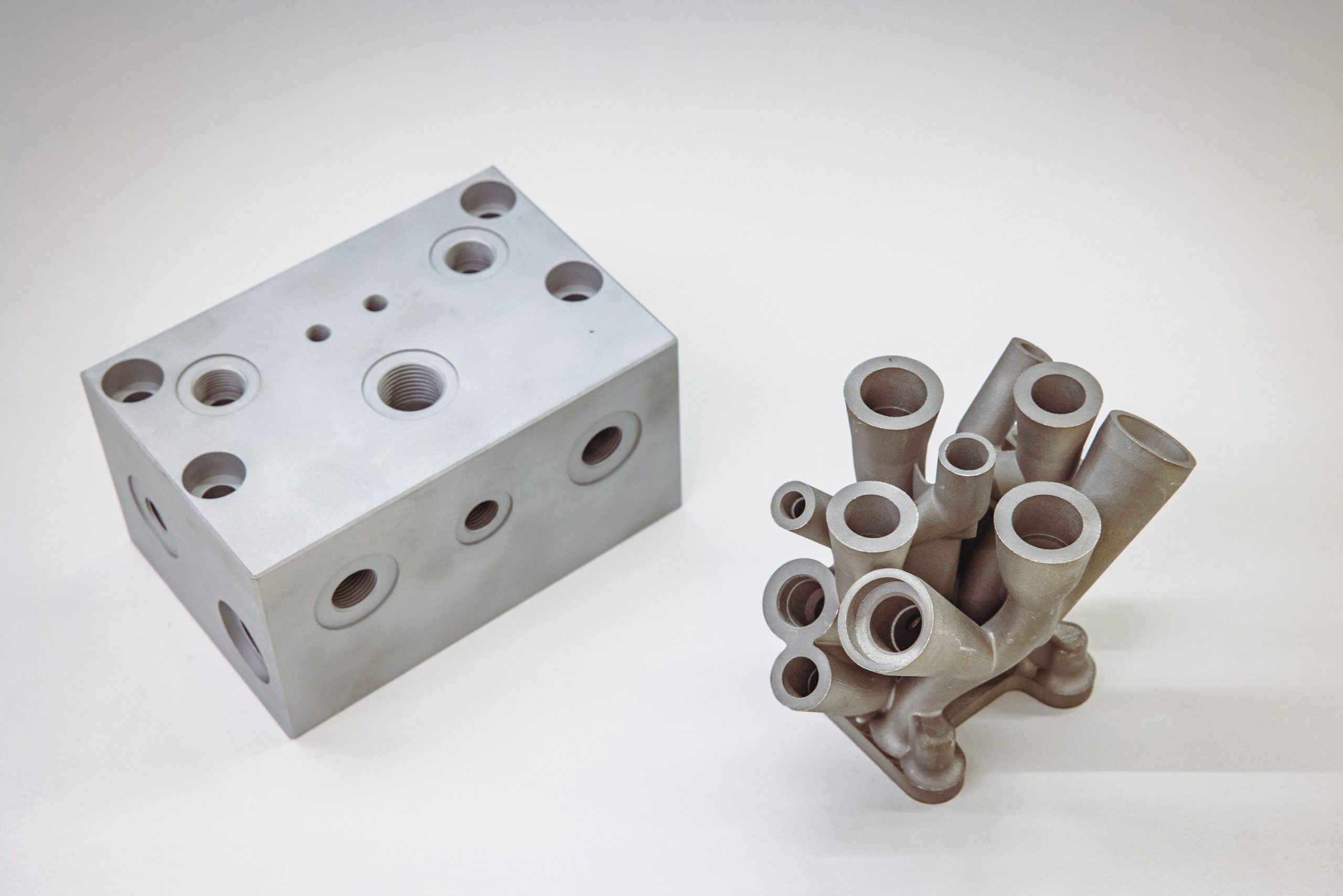
„Deutschland hat am weltweiten CO₂-Verbrauch einen Anteil von gerade mal zwei Prozent. Selbst wenn wir es schaffen, unseren Ausstoß auf null zu senken, hat das für das Weltklima kaum einen Effekt“, sagt Beyer. „Wir können als Vorreiter nur etwas bewirken, wenn wir Technologien entwickeln, die von anderen Ländern eingesetzt werden, um auch dort die Klimabilanz zu verbessern.“
Corona-Pandemie treibt 3D-Druck-Technologie voran
Corona hat die Forschung in diese Richtung nur weiter beflügelt. Denn die Pandemie hat überall Lieferketten unterbrochen. Es fehlte an wichtigen Materialien oder Ersatzteilen. Das Bergedorfer Institut hat kleine 3D-Produktionsanlagen entwickelt, die in Containern untergebracht sind. Diese Container kann man in alle Welt exportieren, so dass beispielsweise Gaskraftwerke in entlegenen Regionen innerhalb weniger Minuten wichtige Ersatzteile oder Rohre einfach drucken können. So kann massiven Produktionsausfällen vorgebeugt werden, die für die Firmen schon mal zu Umsatzverlusten in Millionenhöhe führen können.
Wichtig war den Forschern dabei eine einfache Bedienung der Anlagen. Ein kurzes Erklär-Video macht es auch fachfremden Personen leicht, die Drucker in Gang zu bringen. So muss nicht immer ein Ingenieur dabei sein, wenn Ersatzteile ausgedruckt werden. Als Wissenschaftssenatorin Katharina Fegebank (Grüne) am Donnerstag in Bergedorf auf dem Bildschirm das grüne Feld „Bauprozess starten“ bedient, legt der Roboter drinnen im Container sofort los. Es blitzt, es rattert. Funken sprühen. Nach 40 Minuten ist der Flaschenöffner, den der Roboter Schicht für Schicht auf einen Ring gegossen hat, fertig.
Weiterer Vorteil: 3D-Druck schont die Ressourcen
„Die 3D-Druck-Technologie hat als Querschnittstechnologie ein enormes Innovationspotenzial“, so Fegebank. „Sie ermöglicht nicht nur völlig neuartige Bauteilkonstruktionen mit smarten Eigenschaften sondern auch eine gänzlich andere Fertigungsinfrastruktur.“ Die dezentrale Produktion nach Bedarf beispielsweise von Hilfsgütern in Krisengebieten sei besonders geeignet, einen strukturellen Wandel in Wirtschaft und Gesellschaft herbeizuführen.
Das könnte Sie auch interessieren: Deutschlands erstes Wohnhaus aus dem 3D-Drucker
Neben der Energieeffizienz ist die Schonung von Ressourcen ein weiterer Vorteil der 3D-Druck-Technologie. Denn flog früher beim Fräsen eine gewaltige Menge an Material einfach als Späne oder Staub in die Luft, wird jetzt ganz gezielt nur das aufgebaut, was genau gebraucht wird.
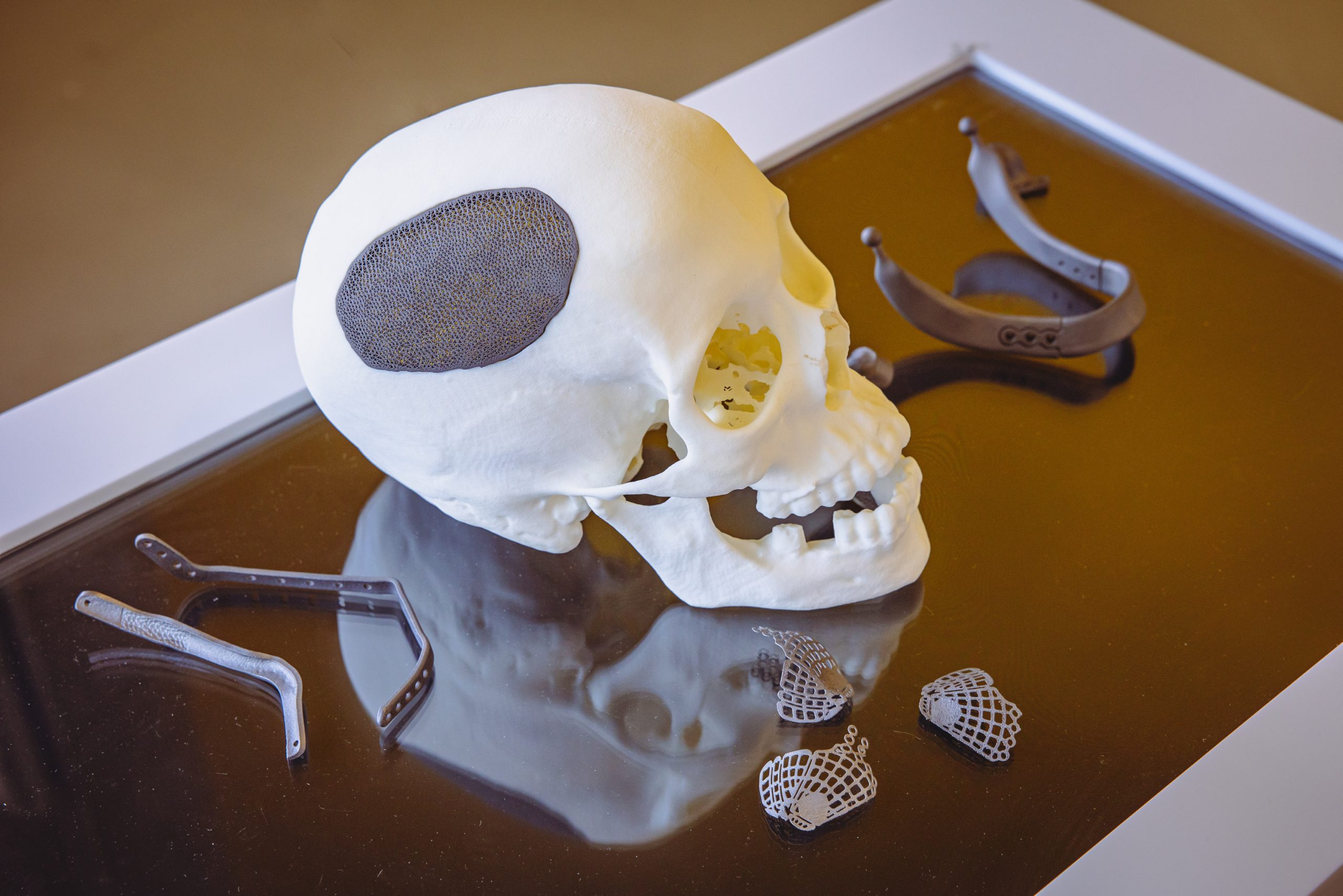
Künstliche Prothesen aus dem Drucker
Neben Bauteilen für die Luft-, Schifffahrt oder Automobilindustrie ist auch die Medizintechnik ein wichtiger Schwerpunkt des Bergedorfer Instituts. So können die Maschinen beispielsweise Menschen helfen, die nach einem Unfall ein Loch im Kopf haben. Per Künstliche Intelligenz wird genau das passende Schädelteil berechnet und dann vom Roboter ausgedruckt. Auch Kieferprothesen, Hüftpfannen oder Augenhöhlenboden, die nach einem Jochbeinbruch benötigt werden, können so produziert werden – alles aus Titan. Im Oktober wird das Fraunhofer Institut dazu eine Kooperation mit dem UKE und der Helmut-Schmidt-Universität starten. Professor Beyer: „Im Verbund können wir viel mehr erreichen.“
Anmerkungen oder Fehler gefunden? Schreiben Sie uns gern.